Check it out, we made a custom battery cable today.
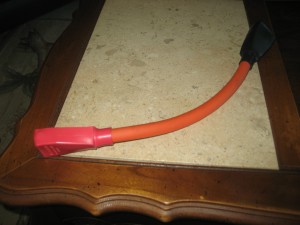
12 incher, a bit longer than needed
I got my new shipment of battery terminals on Thursday. I mailed the parts back for exchange on Saturday, all the way to Utah. I’m very happy with the service I’ve received from EVSource. After today’s experience, I think I’ll need to place another order with them to take advantage of their tool rental program. Here’s the scoop:
I’d just come home with a pair of high-leverage Klein cable cutters from Home Depot. I stopped at Sears a few times to get a pair and their cable cutting selection was mostly cleared out, so I was happy to find them at Home Depot, meant I didn’t have to mail-order and wait.
Anyhow, I figured I had my new terminals, terminal covers, wire (seems to be called “cable” once it’s 2/0 size so I better start to if I want to seem like I’m professional-like), heatshrink and cable cutters. Might as well make a battery cable, right? I thought so.
I pulled up the specs on my batteries, some paper and some theory a guy name Pythagoras figured up. Take the distance between the terminals squared plus the width of the battery squared and then desquared and I got about 10.85″. I added a smidge for a buffer and measured roughly 12″ out of my 20′ coil of wire.
Back out came my Klein high-leveraged 9″ cable cutters. I found my mark and clamped on. About 15 seconds of claming later I figured I needed to figure something else out since I couldn’t seem to leverage enough on my high-leveragers. I pulled out some 1′ socket extensons and deep sockets that fit snug on the handles and gave that contraption a squeeze, but to no avail.
I then thought to put the handle between the gap on my Craftsman clamping professional work table. That did the trick pretty easy – basically like putting the handles inside a vise. So now I had a cut to length cable. Used the cable cutters to slice through the outer sheath of the cable and pulled it off.
Assembled it all together so we had the terminal covers on, then the heat shrink, then the terminals. Then I realized I had the black terminal cover on the side with the positive terminal. Good thing it wasn’t crimped yet – you need to QC these things.
I’d previously found a boat store locally that provides a benchmounted crimper for making battery terminals. So we loaded into the gasmobile and drove on up there. Once there I took a good look at the crimper and realized it wasn’t quite big enough for 2/0. Figured I give it a whirl anyways.
It closed down pretty easy – I’d even say it was high-leveraged. We took a look at the terminal and it actually went through the lug and exposed the copper cable a tiny bit. We went ahead and did the other side too being careful not to cut through. I’ll keep a close eye on the terminal and make sure it doesn’t get hotter than the others indicating the connection isn’t very good.
We headed to the battery store after that to see how Pythagoras did with that math. We set 2 batteries wide to side like they’ll be in Trans Amped and the battery was about 4″ longer than it needs to be… That’s more than a smidge so I blame Pythagoras. Lesson learned so I made a note of how long the next cables should be.
Got home, fired up my new heat gun (located in the paint section, not heat shrink section of our neighborhood Ace) and shrunk the wrap around the crimps. All done.
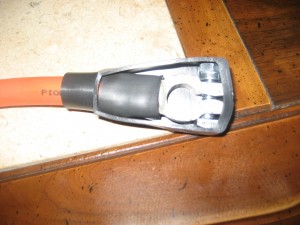
I haven't had many pictures lately, so here is another.
Overall it should go pretty well since I figured out the kinks. The only other thing was the terminal covers fit snug on the cable, so when the heat shrink is added it gets mighty tight, Barn. Sorry, we’re watching Andy Griffith right now.
Also bought some misc. wiring and connecters for my low voltage system.